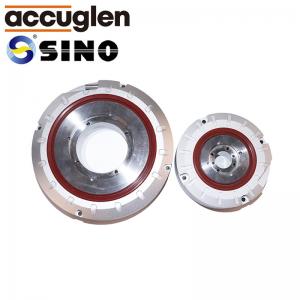
Add to Cart
SINO Sealed Incremental Angle Encoders AD-60MB-S18 ISO9001 For Milling Lathe Grinding Optical Angle Encoder
ISO9001 Sealed Absolute Angle Encoders AD-100MA-C29 Granding optical angle encode For Milling Lathe
The term angle encoder is typically used to describe encoders that have accuracy from ± 5” to± 10” and a line count above 5000. Angle encoders of choice when angle measurement in the accuracy of a few seconds is required.
Safety Notice
This instruction manual is to guide technical personnel participating in installation and commissioning. Carefully read this instruction manual before installing and operating this product. Warranty will be lost due to unauthorized modification and unallowed utilization.
Nordon Corporation also provides linear scale, encoder, etc. required for other different applications, including:
specifications
ITEM | AD-100MA-C29 |
Shaft size D1 | 100g7(-0.010/-0.040) |
D2 | 120 |
D3 | 200 |
D4 | 188 |
D5 | 115 |
D6 | 106 |
D7 | M100*1 |
D8 | 180 |
H1 | 39 |
H2 | 3.5 |
H3 | 32.5 |
H4 | 6.5 |
M | 4*M4*30 |
Photo
Advantages of enclosed incremental linear encoders
The sealed incremental linear encoder measures the position of the linear axis without additional mechanical transmission. All feed mechanisms are included in the position control loop through the linear encoder, and the mechanical motion error of the control loop is detected by the signal acquisition and processing system. The linear encoder reads the head and corrects it from the control, potentially eliminating several sources of error:
1. Positioning error caused by thermal expansion of the ball screw
2. Game bug
3. Motion error caused by ball screw pitch error
Therefore, the enclosed incremental linear encoder is an indispensable basic technical resource for high-precision, high-speed processing machinery.